Blog
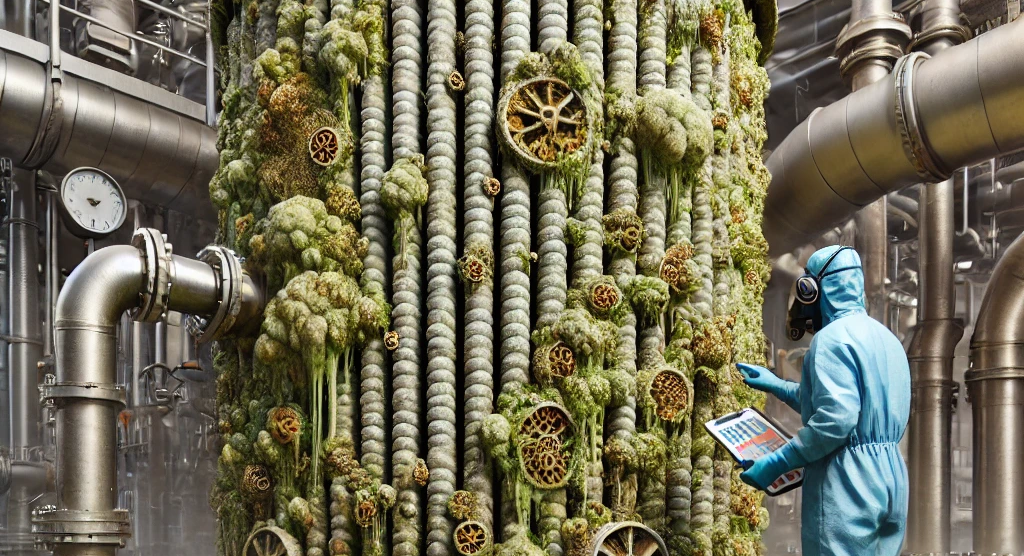
Biofouling in Cooling Tower Water Systems
Causes, Problems, and Effective Prevention
Cooling tower systems are critical in various industries, providing efficient heat dissipation. However, biofouling remains a persistent challenge, affecting system efficiency, increasing operational costs, and leading to potential equipment failures. In this article, we explore the causes, consequences, and preventive measures for biofouling in cooling tower water systems, backed by real-world examples and advanced monitoring technologies.
What is Biofouling?
Biofouling refers to the accumulation of microorganisms, including bacteria, algae, and fungi, on cooling tower surfaces. These biological deposits form slimy biofilms that reduce heat transfer efficiency, promote corrosion, and increase energy consumption.
Causes of Biofouling in Cooling Towers
- Nutrient Availability: Cooling water often contains organic matter, phosphates, and nitrogen compounds that promote microbial growth.
- Warm and Humid Conditions: Cooling towers provide an ideal environment for bacteria and algae to flourish.
- Stagnant Water Zones: Dead zones in the system encourage microbial accumulation and biofilm formation.
- Inadequate Biocide Treatment: Poor selection or under-dosing of biocides leads to ineffective microbial control.
- Airborne Contamination: Dust, pollen, and airborne microorganisms contribute to biofouling.
- Recycling of Water: High cycles of concentration can lead to increased microbial load.
Problems Caused by Biofouling
- Reduced Heat Transfer Efficiency: Biofilms act as insulators, reducing the ability of heat exchangers to dissipate heat.
- Increased Energy Costs: A biofilm layer of just 0.5 mm can increase energy consumption by 10-20%.
- Corrosion and Equipment Damage: Microbiologically Influenced Corrosion (MIC) can severely damage cooling system components.
- Clogging and Reduced Water Flow: Biofilms can clog nozzles, pipes, and heat exchanger tubes, reducing operational efficiency.
- Legionella and Health Risks: Cooling towers with biofouling provide an ideal breeding ground for Legionella bacteria, posing health hazards.
Real-World Example: Cost of Biofouling in an Industrial Cooling Tower
A manufacturing plant using a 10,000 TR cooling tower observed a 15% increase in energy consumption due to biofouling.
- Pre-biofouling scenario: Energy consumption = 100,000 kWh/month
- Post-biofouling scenario: Energy consumption = 115,000 kWh/month
- Additional energy cost: 15,000 kWh/month × Rs.10 /kWh = 1,50,000/month
- Annual loss = Rs. 4,95,00,000 due to biofouling
Preventive Treatment Programs
- Chemical Treatment
- Oxidizing Biocides: Sodium hypochlorite (NaClO), chlorine dioxide (ClO₂), bromine compounds
- Non-Oxidizing Biocides: Glutaraldehyde, isothiazolinones, polyquaternary amines
- Bio-Dispersants: Help break down and remove biofilm deposits
- Physical Control Measures
- Ultraviolet (UV) Systems: Effective against bacteria and algae
- Ultrasonic Treatment: Disrupts microbial cell walls, preventing growth
- Hydro cyclones and Filtration: Remove suspended solids that serve as microbial nutrients
- Microbial Monitoring and Control
- Regular ATP Testing: Measures microbial activity in real time
- Dip Slide Testing: Provides a quick visual confirmation of microbial contamination
- Online Biofilm Sensors: Detects early biofilm formation and triggers automated responses
Advanced Monitoring Technologies
- Real-Time Biofilm Monitoring
- Uses electrochemical or ultrasonic sensors to detect biofilm formation
- Sends alerts for corrective action before fouling becomes severe.
- IoT-Enabled Smart Sensors
- Measures biocide residuals, pH levels, ORP (Oxidation-Reduction Potential)
- Provides remote monitoring and control of chemical dosing
- AI and Predictive Analytics
- AI-based pattern recognition predicts potential biofouling events
- Helps optimize biocide dosing schedules for cost-effective treatment
Conclusion
Biofouling in cooling tower water systems is a costly and operationally challenging issue. A well-structured preventive maintenance program combining effective biocides, physical treatment technologies, and real-time monitoring can significantly reduce biofouling risks.
With the advent of IoT and AI-driven predictive maintenance, industries can now proactively manage biofouling instead of reacting to problems after they arise. Implementing smart water treatment solutions ensures long-term efficiency, cost savings, and operational reliability in cooling tower systems.
Need Help with Cooling Tower Water Treatment?
At Geopure Aqua Technologies, we provide expert solutions for cooling tower biofouling control. Contact us for customized treatment programs that maximize efficiency and reduce costs.
Visit our website: www.geopure.co.in | www.geopureaqua.com